So far, digital twin technology has mostly been used as an alternative to traditional climbing to collect data. In other words, it was an inspection tool to deliver traditional reports, like closeout reports, construction documents, etc. However, even in their limited scope, these tools helped significantly to educate the industry about the available options.
At its core, these services used photogrammetry to generate 3D models from drone-captured imagery. As expected, these models were great for visualization but didn’t serve the business purpose. Global economy ensued setting up back-end offices elsewhere in the world to manually create and deliver those reports.
Security concerns
Processing through back-end offices had unintended consequences, including data residency and data privacy violations. In some cases, businesses were unaware of the process and were exposed to unauthorised usage of an organisation’s data. As good and reliable data is becoming the foundational component to the success of a business, organizations are increasingly concerned about exposing their data for unintended purposes. So, it raised the legitimate question of data ownership. Instead of service providers, organisations like TowerCos and MNOs should own the data of a tower digital twin.
Busting the myth
When we started the journey of digitisation of thousands of towers, we needed to plan to deliver long-term value propositions to the business. For that, we needed to break the mold of an “inspection tool,” proving that an inspection report is just a snapshot output of a tower’s digital journey.
There is also a common misinterpretation of equating a point-cloud model to a digital twin. To put it simply, a point cloud is a photogrammetric output to mimic a 3D physical object with a cloud of densely populated points. This is a popular technology because of its simplicity. However, it doesn’t guarantee the generation of geometric shapes like a convex profile of an antenna, rather it draws points for users to imagine and create shapes. Figuring out a shape from a point cloud can be complex and the presence of multiple objects in the vicinity can further convolute shape identification. Reality mesh is the perfect solution to overcome this challenge. By generating meshed models, this technology generates surfaces and volumes of different objects. A visualizer can efficiently render different geometric objects to their accurate shapes, ensuring object segregation for downstream workflows.
The journey
It shouldn’t come as a surprise that when we started the project in November 2023, we were grappling with unknowns and uncertainties. However, we were certain of our purpose, how the organisation can gain value through digitization.
Security
One of our early goals was to ensure data security. As a public company and being SOC 2 compliant, we offered Bentley’s iTwin platform that leverages Microsoft Azure cloud. As the towers are in the USA, we decided to use the East US data center for all data storage and processing. The platform comes ready with Role-based access (RBAC) to ensure data protection from unintended editing or even corruption.
The problem of volume
The telecom business is all about volume. When you need to digitize tens of thousands of towers within a few months, you must have a robust backend that can scale up (and down) for seasonal needs. For example, data collection can be challenging in winter, but it can rapidly increase in Spring. OpenTower iQ’s scalable processing was the perfect recipe for digitizing thousands of towers per month.
The other aspect of digitization is time. The massive volume of data transactions could easily clog the system and significantly slow down the throughput required for each day. We quickly realized that the entire process must be automated. OpenTower iQ’s “reality model generation” web app was meant for that. It automatically selects appropriate settings for tower types and chooses the right dataset for optimum processing speed. Bentley released a new set of APIs for asset registration, assigning teams with correct RBAC permissions, uploading data, and triggering the model generation. The result was magical, automated, and scalable processing to produce hundreds of models per day.
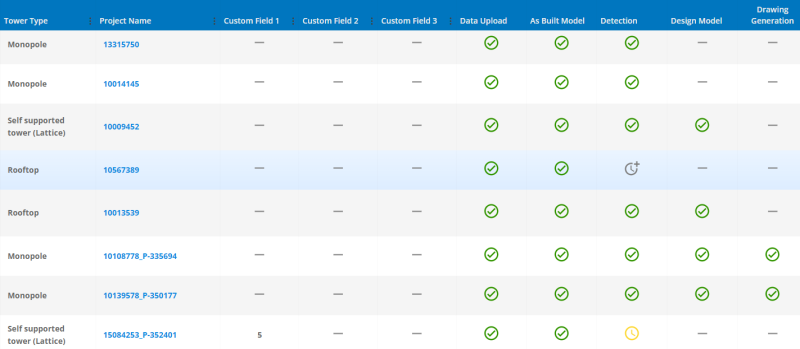
Garbage in, garbage out
A process can only be scaled by software if the input adheres to a minimum standard. OpenTower iQ is drone agnostic and supplies a well-defined capture guideline. However, these types of projects need massive deployment of drone pilots for data collection. Each pilot is different and there are obvious technical as well as practical challenges, like obstructions in the site due to vegetation or a drone’s interference with the RF signals remitting from that tower. Challenges due to lack of experience on how to maintain equidistance and concentric orbits, etc. The only option was to use an automated flight path optimized for OpenTower iQ’s scalable processing.
The other challenge in ensuring data quality is the lack of consistent georeferencing to ensure continuity. Drone imagery is typically georeferenced with GPS coordinates. However, due to numerous challenges, like battery swaps, obstructions, difficulties in manually positioning a drone at the last position, etc. georeferencing isn’t always consistent. Good and experienced pilots can ensure georeferencing but managing hundreds of pilots adhering to the same standards can be incredibly challenging. The obvious result was inaccurate data that clearly affected the precise measurements and defeated one critical use case, the reconciliation of the inventory database. We adopted a known geo-correction technique using RTK-empowered devices. The result was accurate models that could confidently verify and even challenge historical data, including RFDS documents. It solved the industry’s biggest pain point, unreliable equipment inventory data.
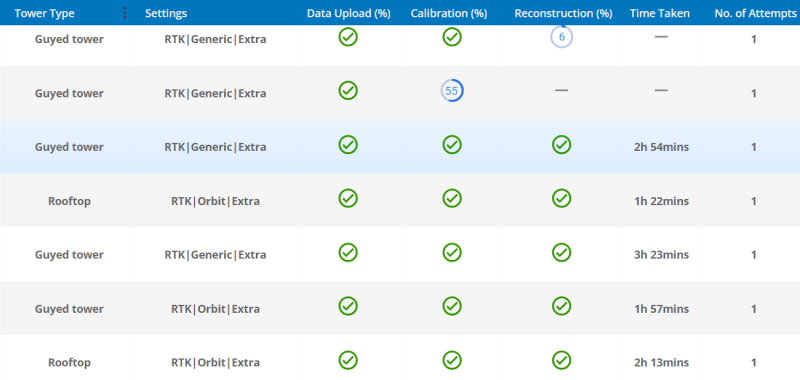
The bold new world of Artificial Intelligence
Obviously, everyone talks about AI and how it can change the world. However, AI isn’t a giant monolithic technology, rather AI can be developed to solve specific problems. So, it’s important to understand what we are trying to solve and how practical it is in terms of time and cost. I discussed this topic in an earlier article, Empowered Digital Twin. It’s still an emerging technology and OpenTower’s AI-first strategy proved to be the differentiator for the unprecedented success of this tower digitization project.
Since its inception, OpenTower iQ’s AI technology has been based on 3D models. It helped to extract dimensions in 3D space and classify different objects, including equipment, bracing, section shapes, ladders, mounts, feeders, etc. Our latest innovation in determining the shapes of equipment saved thousands of person-hours in classifying manufacturers and model numbers of equipment. It was the perfect trigger to automatically generate high-LOD BIM models satisfying a key requirement of the project. So, we could create a high-quality BIM model automatically from just drone imagery. Needless to mention, it saved tens of thousands of person-hours and millions of dollars.
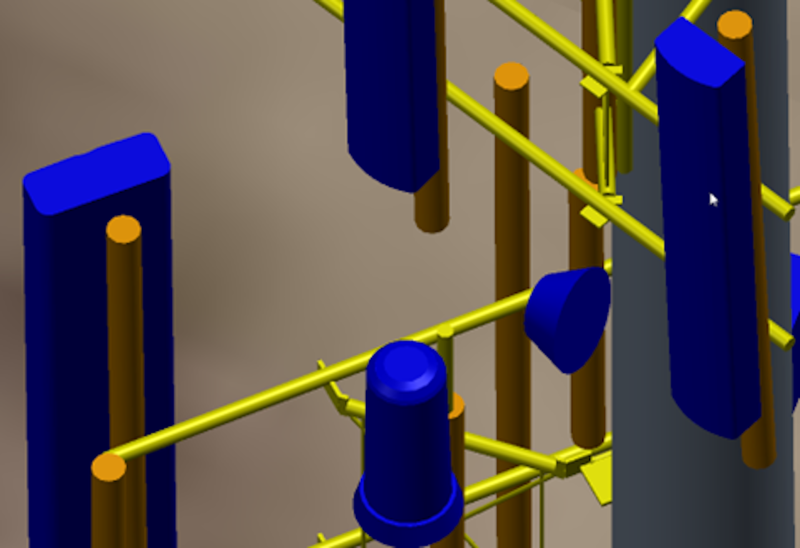
A collaborative environment for SME review
As with any innovative technology, subject matter experts (SME) were often critical and needed proof to earn their trust. OpenTower iQ provides a collaborative environment for users to check, modify, and save different artifacts of a tower and the associated ground. Once a SME reviews and confirms the quality of data, the downstream workflow, like producing construction documents, was completely automated. It solved another industry pain point which is data silos and more importantly, inconsistent data for the same site among different departments. It served the purpose of one source of truth.
Getting the towers ready for the next stage
One of the critical aspects of tower maintenance is to keep up with the evolution of newer technologies supporting the ever-growing need for data and speed. Towers must support bigger and heavier equipment for collocated operators. The purpose of this project was to upgrade the network infrastructure of an operator. Obviously, the first step of digitization towers was to understand the current condition of the towers along with existing equipment inventory. It also automatically provided a platform for RF planning on a 3D reality model, ensuring data integrity. OpenTower iQ could automatically generate pre-construction drawings, a requirement of the project.
The new models are now ready with the existing and proposed loading. Version changes were enabled to audit the changes at any stage of the project and for historical purposes. However, the most important benefit was to have a model ready to ingest post-construction drone imagery to automatically confirm the quality of installation and report mismatches (if any) between the proposed and the installed loadings.
Client branding
Branding was an important aspect of our client’s success in marketing their services. Being a software company, we collaborated with our client to automate API-driven backend interactions for easier access to models, reports, files, etc. without leaving our client’s platform.
Observations and conclusion
They say that hindsight is 20/20. Looking back, this project’s success (or failure) was heavily hinged on the performance of the AI technology developed for the detection and classification of tower objects. It ensured high-fidelity data extraction enabling automation for the downstream workflow, including required reports and drawings. It was a risk worth taking, especially with the possibility of significant reduction of health hazard for climbers. It’s also worth mentioning saving millions of dollars, avoidance of human errors, and reducing tens of thousands of person-hours. Models were generated in hours and reports were generated instantaneously, helping our client to deliver the projects at a record pace.
Key Numbers
Number of digitised towers: 25,000
Average image dataset size for each capture: 20 Gpx
Average reality model generation time: 4 hours
Detection and classification success rate: 91%