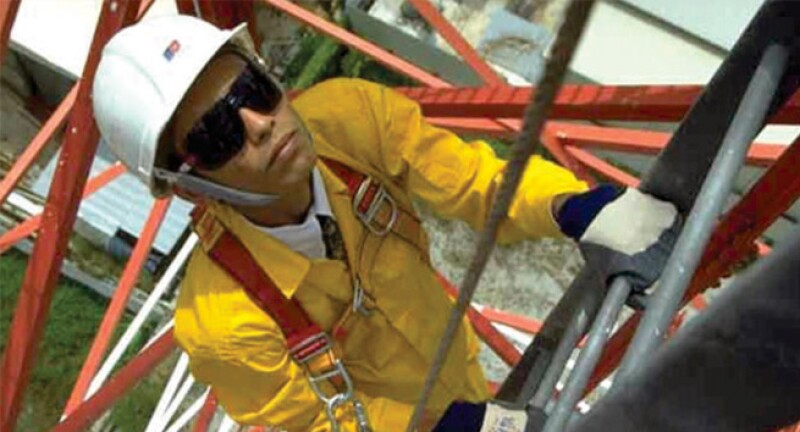
Read this article to learn:
Health & safety is a mindset, and it needs to change
On-site teams need the appropriate training and procedures
It’s not just about the right training, but the right equipment too
Training and equipment comes at a cost
HSE needs a policy framework
Digitisation might be the key
Last month I had the privilege of being invited to attend the 2023 annual Lifting Safety to New Heights (LSNH) conference, held just outside Dakar in Senegal. LSNH is a two-day working group that has been running since 2019, previously held in several African countries including Tanzania, Kenya, Ghana and South Africa. LSNH is a platform designed to lead the conversation on the key risks associated with working at height to drive change within the African telecom industry.
The event is organised by four sponsoring firms; leading international OEM Nokia, pan-African towerco Helios Towers, technical consultancy UIRTUS, and health and safety training platform Gravity Training. Over the two days, key speakers from the sponsoring companies, as well as local Senegalese organisations including local MNO Sonatel (Orange Senegal) and the Ministry of Communications, shared insights and practical solutions on how to lift safely to new heights.
Attendees, many of whom were suppliers for Nokia and Helios towers, as well as local firms including local MNOs Onatel and Free Senegal, heard from a series of panels, presentation, roundtables and practical demonstrations that discussed the risks on-site teams are exposed to and the training procedures, equipment and technology that can help mitigate them.
This article compiles six key takeaways from LSNH, touching on a broad range of challenges and solutions that were discussed across the workshop.
Takeaway 1: Health & safety is a mindset, and it needs to change
The most repeated phrase used by speakers and attendees at LSNH was ‘changing hearts and minds’. In Africa there is a common attitude by on-the-ground climbers and supervisors to get the job done over doing the job safely. Managers play a big part in this mindset, who can chastise climbers if they don’t complete the task, and often prioritise performance over procedure.
In Africa, there is also a cultural mindset that is more open to taking risks when tasks need completing and acts as a barrier to the implementation of top-down health & safety standards. Maintenance teams are used to transversing dangerous roads and moving equipment using precarious means. Will Richardson-White, Group Head of SHEQ for Helios Towers, explained in his presentation that “its normal to have to make dangerous decisions because management needs to get things done, regardless of whether it was done safely or not”.
Attendees were shown several videos showing dangerous work practices, including using flimsy wooden boards as a ramp to transport a vehicle onto a boat, and manually lifting antenna equipment up to the top of a tower via a rope pulled by hand. So how do you control the willingness of a maintenance worker to take risk? asked Nokia's Country Manager for Senegal Abdu Lo; you make safety a priority, beyond business performance.
Of course, a healthy mindset doesn’t just come from climbers themselves, but instilled by those responsible for training and overseeing them. The risk of injury or fatality when climbing makes on-site maintenance a high-stress environment, so there were claims from both speakers and audience members for supervisors to encourage open discussion about how safe climbers feel.
While work pressure might help get a job done quickly, it can create a habit of getting things done efficiently over safely, so riggers don’t often feel comfortable raising health and safety concerns, leading to more stress and ultimately more risk. Encouraging managers to be supportive, helping create opportunities for staff to openly communicate their concerns, providing constructive feedback and instilling self-confidence in climbers are call simple but effective practices supervisors can implement to create a safer work environment.
Takeaway 2: On-site teams need the appropriate training and procedures
Changing the mindset around safety is one thing, but to achieve this the industry needs to create the proper processes and procedures to implement change.
One major barrier to this is top-down implementation. Health and safety might be brought up in the meetings and strategy discussions of senior leadership, but is this being communicated in an effective way at grassroots level? Climbing managers don’t always understand the HSE practices that are being implemented by leadership, or how to execute them.
Communication networks, such as the NOCs, can often prioritise fixing the problem with resolving safety issues later. Even if management is making HSE a part of their strategy, there needs to be better management of these practices in the field.
A leading cause of this failure of communication is education and training. Abu Lo, Nokia's Country Manager for Senegal, discussed this point at length as many African countries, including Senegal, do not have proficient educational institutions.
Field technicians might have all the certifications necessary for the job, but often lack the educational background to be able to understand and implement new management protocols; “It’s important to teach them the importance of safety practice, not just how to do the job right”. Lack of training was also highlighted as one of the three major causes of on-site accidents.
Not just education, but the language barrier can be a huge issue in training and procedure as well. Participants discussed this at length in one of the roundtable sessions, as most riggers don’t speak either English or French but one of the many native languages found across the continent. Senior and local management need to consider language barriers when communicating procedures and providing training, as well as the educational competency to understand them.
But it’s not just communication that is important, but technical know-how as well. Spencer Crawford-White, Technical Director for UIRTUS, explained how as the load of active equipment increases with new technology and colocations, it's critical that new lifting procedures and structural assessments are used. On-site teams need to understand exactly what the capacity of the load is to undertake a structural analysis before planning how it will be lifted safely into position.
Spencer Crawford-White gave several examples of poor lifting procedures, including using a tired and some wood to fasten a beam in place at the top of the tower to lift equipment, reducing structural integrity of the tower and risking the equipment dropping at height.
While this may seem like a technical complex challenge, Nokia provides a standard for structural integrity with clear steps on how to safely lift equipment on sites for free. With simple and easy-to-understand processes already out there, it now needs to be applied down the contractor change. “By implementing the right practices and equipment you have safer people, quicker deliver and reduced costs”.
As Spencer discussed the importance of technical procedure and assessment, using the right equipment to lift loads is also critically important. Riggers need to have the right tools to lift equipment, as well as to understand how to use them.
Takeaway 3: It’s not just about the right training, but the right equipment too
Another example that was given was an incident where a team was using a mechanical advantage to lift equipment, but the load was more than the equipment could take, which risked the antenna falling and landing on people, causing loss of value, time and potentially lives. Alongside lack of training, Abu Lo also highlighted misfit equipment as another leading cause of accidents, as teams which do have equipment may not correspond to the activities they are being used for.
The equipment specialists on-site during LSNH was Gravity Training, who have been offering worker height and rigging training in Africa since 1999. The Gravity team gave a demonstration of how even simple pieces of equipment, such as a pully system, could dramatically help make lifting safer and more efficient.
While a single pulley system still risks injury if the equipment falls and the rigger attempts to grab the rope, using multiple pulleys with more rope to disperse the weight might be require more upfront investment, but improves worker safety, efficiency and reduces the number of people needed on-site.
Under the blazing mid-day sun, attendees were also escorted to a nearby telecom tower, where Gravity ran a demonstration on how to safely lift heavy loads using a diesel mechanical lifter, as well as how to safely rescue riggers who get stuck at height. What matters, according to Gravity, is that on-site teams have all the right tools they need for every occasion; shackles, pulleys and swings, as well as the correct practices to use this equipment properly. By using equipment, on-site teams can reduce the number of people needed to safely build or maintain a site, reducing costs, saving on resources and reducing fatalities by limiting the number of people who are at risk.
Takeaway 4: Training and equipment comes at a cost
Presentations and demonstrations from Nokia, Gravity Training and Helios Towers clearly outlined the benefits of proper training and equipment on safety and efficiency, but one clear voice of concern from attendees was cost.
Among several roundtable discussions, cost and procurement were raised multiple times. The first challenge is the cost of training; even local African suppliers, such as Gravity Training based in South Africa, are expensive for local teams in poorer countries. One suggestion was for companies like Gravity or Delmec to train up trainers themselves who can offer cheaper services in poorer markets to make it more affordable. However, this would be a long-term investment and would take time to materialise.
It can also be hard to find the budget in a contract to allocate resources to HSE reequipment and training, as many rigging teams are small local firms, sometimes individually contracted. Some contracts include a 5% capital allocation for safety equipment, but this only works for larger contracts, as smaller ones often don’t cover this.
There is also the issue of work-load planning, with contractors concerned about investing in equipment without a clear workflow pipeline that can support the upfront investment in HSE. Helios Towers have implemented a system where contractors can claim back costs of safety tools and training for a job, but clients need to provide more of a heads-up about future work.
That cost of equipment can also be hugely disproportionate to local markets, as high-quality equipment is expensive and usually imported. It is challenging to manufacture EN-standard equipment as many manufacturers on the continent don’t meet the necessary standards.
Gravity has found a French manufacturer in Madagascar who does and has been able to attempt to match prices to the African market, but there aren’t enough manufacturing hubs across the continent to do this at scale. If more local manufacturers meet EN-standards, safety equipment could be produced in local markets which would reduce the price.
Takeaway 5: HSE needs a policy framework
LSNH plays an important role in facilitating dialogue and providing insights into the importance of HSE in the tower industry, but beyond this there is very little industry standardisation around health and safety. Nokia pointed out that there are no standards for HSE practices, and while lots of industry players are trying to implement their own internal procedures, the lack of involvement from authorities limits how unified this approach is.
Big players in the industry need to be providing the framework for implementing standards, and Nokia and Helios Towers are helping to drive this narrative through LSNH, but more work needs to be done beyond this.
A representative from the Ministry of Communications attended the event, although it was to his surprise that LSNH was about health and safety of the telecom tower networks, rather than cybersecurity. Despite this slight hick-up, Senegal’s Ministry of Communications expressed his keen interest in making HSE practice play a greater role in the regulatory framework, as inspectors are already doing to tower sites to assess risks of spectrum and site security.
He also mentioned that while the industry is not currently in open discussion with the regulator, key players such as Nokia are already enforcing contractors follow their HSE practices and expressed interest in carrying this framework to ensure MNOs and their suppliers also respect proper safety practices.
Industry standardisation was a recurring theme at LSNH, as multiple attendees raised the issue of a lack of telecom regulatory framework around HSE, which makes it hard for individual organisations to implement policies with regulator or broad industry support. One major challenge is the perception of HSE standards as a competitive edge, which negatively impacts the creation of broad industry practices.
Attendees agreed that a base levels of HSE practices across the industry is extremely important, especially as contractors can change their HSE practices depending on what their client demands, causing them to benchmark their health and safety standards to the lowest standard.
This is why organisation such as LSNH play such an important role in the industry, as HSE management often varies from company to company, so platforms that bring together the ecosystem to benchmark and share best practices is so important, and more of these workshops need to take place.
Takeaway 6: Digitisation might be the key
The challenges raised around poor health and safety practise that were raised across the event were usually due to two factors; on-site teams using legacy processes and equipment, and management not having the tools to understand the actions of field workers.
Due to the highly outsourced nature of the tower industry, digitisation of safety systems is key. But the challenge for HR and management is the inability to oversee front-line operations directly. Oversight platforms can also be used to monitor the actions of contractors as well as internal teams to ensure they put in place the HSE practices required by their customers. Many contracts require that on-site workers have a certain level of training and qualifications, but without any system to check this often goes ignored.
Helios Towers has implemented an IBMS tool to great success in order to overcome this issue. Field teams for Helios do an average of 17.5 million kilometres per year of driving. As the entry threshold for driving in Africa is very low, and road accident risks are high, IBMS provides a critical element of oversight looking at driving metrics including harsh breaking, acceleration and oversteering to assess how safely field workers are driving. Automation is a big part of Health and Safety, according to Nokia, who are also using IBMS platforms for sire control to oversee the management process.
Drones were another key piece of technology that can help mitigate the risks for on-site teams by both reducing the need for tower climbs. Attendees were given a demonstration about how to fly a drone and the value of being able to efficiently gather accurate data to reduce tower climbs, manpower and time.
Using drones, and the digital twin platform that allows for companies to create digital copies with accurate data and scanning of a towers structure and equipment, helps reduce the often-inaccurate data gathered in-person due to rushed work, poor training, misreading or any other human error. According to Spenser Crawford-White, 50% of gathered data is inaccurate and if often not updates, corrected or inputted properly in the system.