Tough new EN standards are now in force for vertical fall arrest systems. So how does your equipment measure up? Is it compliant? Or are you putting workers at risk – and risking your company’s bottom line and reputation at the same time?
When you’re responsible for the safety of workers climbing vertical structures like wind turbines and telecomms towers, there is a lot resting on your shoulders. It’s your responsibility to help make sure workers return home safely to their families at the end of the working day. And we appreciate that’s a big responsibility, because despite all the advances made in recent years in fall arrest systems, personal protection equipment and health and safety requirements, climbing tall structures remains seriously dangerous work.
Could you be the next HSE statistic?
Only last year, for example, two workers unfortunately fell to their death within the space of two weeks while working at Scottish wind farms.
The latest health and safety statistics published by the Energy Institute for UK offshore wind farms show that working at height remains a key risk for the industry. The figures show that in 2016, there were, thankfully, no fatalities. However, there were 737 health and safety incidents, including 110 incidents working at height. Half of the 110 working at height incidents were classified as high potential and four working at height incidents led to lost work days. Overall, 248 of the 737 incidents were reported as high potential and 23% of these occurred while working at height.
Meanwhile, it’s a similar story in the telecoms industry, as falls from height continue to be a big risk for workers in the telecomms industry. Figures for the US telecomms industry show that there were 13 fatalities in 2013 and 11 in 2014.
Complying with the latest standards
Given the continuing risks of working at height, asset owners and all those responsible for health and safety will want the peace of mind of knowing that their vertical fall arrest systems are fully compliant, ideally with the very latest standards. But understanding health and safety requirements is not always easy. EN standards are frequently revised and updated. This can be a long process and often interim standards are introduced. So how do you know whether you are compliant and how can you best protect your workers involved in working at height?
The new standard for vertical fall arrest systems
The all-important standard that you need to be aware of is EN 353-1:2018, the standard relating to the testing of vertical fall arrest systems. This standard started its life as EN 353-1:2002. However, the death of a 19-year-old construction worker in 2007 led the Health and Safety Executive to review the standard. The worker died when he fell 100 ft down the shaft of a wind turbine under construction.
How the new standard came about
The review by the Health and Safety Executive showed that the standard did not satisfy health and safety requirements. As a result, the EU Commission issued a mandate saying that testing to EN 353-1:2002 alone was not sufficient. Manufacturers then had to test to the interim VG11 sheet as well as EN 353-1:2002, a stopgap measure to ensure that health and safety requirements were being met.
Work to revise EN 353-1:2002 started in 2010 and in 2014 the updated standard EN 353-1:2014 was published.
The role played by global leader in workplace safety – MSA Safety
However, when industry best-practice leader MSA Safety started testing its vertical fall arrest systems against the revised standard, it noticed that there were errors in the cold conditioning tests. It therefore worked with the Standards Authority and recommended amendments to correct the errors. The outcome is the publication of EN 353-1:2018[1].
The tests covered by EN 353-1:2018
EN 353-1:2018 is now live and all new vertical arrest systems should be tested to this standard. Tests include:
Dynamic performance test- testing to check the maximum arrest force
Cold condition testing- checking the locking function in cold conditions
Minimum distance test- testing to replicate the user falling close to the anchor line
Fall back test- this test replicates the user falling back and down
Guide bracket test- testing the strength of the bracket and anchor line and the locking function of the fall arrester in the event of a fall
Sideways fall test- testing to replicate the user falling in a sideways direction
Leaning angle test- testing the locking function of the fall arrester with the anchor line leaning forward and sideways
Static strength requirements- testing to check the overall strength of the system
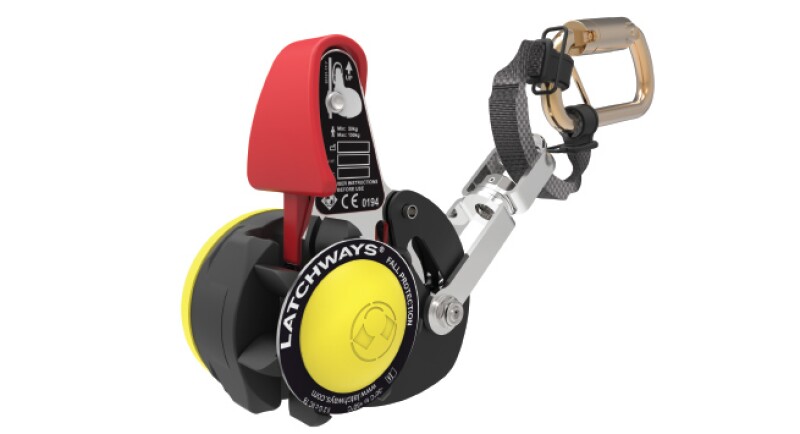
Understanding whether you are compliant with the new standard
So how do you know whether your systems and equipment are compliant with the latest standard? Well, if you have one of the vertical arrest systems manufactured by global safety expert MSA Safety, you can enjoy complete peace of mind. That is because all MSA Safety’s vertical fall arrest systems, even those manufactured before 2002, comply with the new 2018 standard.
"We have tested our TowerLatch and LadderLatch systems against EN 353-1:2018 and are delighted to say that they already meet all the requirements of the new standard. This really is testament to our long-term approach and how we future-proof our products for added longevity, value for money, and ultimately, the highest levels of safety.” says Tim Bissett, Technical Manager at Latchways plc.
“Having said that, we also pride ourselves on adopting a continuous cycle of innovation and staying one step ahead of the market. It’s how we continue to design and deliver the highest level of safety products," he adds.
"As best-practice leaders for working at height equipment, we take safety extremely seriously. Ultimately, lives are at stake here and that’s why, right from the start, we’ve always subjected our systems to extremely rigorous tests. Our aim is to make sure that whatever happens and whatever the conditions, workers using our equipment remain safe."
Check what your system has been tested against
But what if you are using a vertical arrest system made by another manufacturer? Well, if you are using a system manufactured before 2002, then you need to review it urgently. The system may no longer be compliant. If you are using a system installed between 2002 and 2018, then check the life of your certificate. If your system complies with EN 353-1:2002 plus VG11 then you have until 2023 when certificates issued under the PPE Directive become invalid.
The systems that already comply with new standard
The TowerLatch and LadderLatch systems referred to by Tim Bissett are MSA’s Latchways engineered lifeline systems for towers and ladders. TowerLatch is designed for use on virtually any type of power transmission tower including steel lattice structures, towers, masts and monopoles. LadderLatch is the equivalent system for fixed industrial ladders such as those used in chimneys, towers, cranes and silos.
The unique ’starwheel component’
Both systems use the unique ’starwheel component’, giving workers the security of being constantly attached to the system, while also having both hands free to go about their duties. In the event of a worker falling, then the device quickly locks onto the system cable and arrests the fall.
Test to new standard, urges MSA Safety
Meanwhile, MSA Safety is urging other manufacturers to follow its lead and ensure that all their vertical arrest systems are tested to the new 2018 standard.
"As an industry, we have a responsibility to ensure that the products we’re selling are tested to the necessary and relevant standards. After all, we’re talking about making sure that someone goes home to their family at the end of the working day.
"At MSA Safety, we take this responsibility very seriously and that’s why we invest so heavily in innovation, research and development. We want our customers to know they’ve got a fall protection solution they can really trust. And this new standard is a fantastic vindication of all our efforts."
A bit about Tim Bissett
Tim is Technical Manager of Latchways plc and a Chartered Engineer with the Institution of Mechanical Engineers. As part of his role as Technical Manager, he helps develop product standards for personal fall protection equipment.
Tim is a member of BSI Technical Committee PH/5, convenor of CEN/TC 160 Working Group 1, convenor of CEN/TC 160 Working Group 2 and principal UK expert to CEN/TC 160 Working Group 6. In addition to his work with European standards, he is also a member of American National Standards Institute ANSI Z359 Fall Protection Committee.