Microtex is a leading technology company that manufactures industrial batteries for energy storage in Bangalore, India. Established in 1969, Microtex produces in-house specially designed lead alloys, lead oxides, grid castings, pasted plates, injection molded containers, multi-tubular gauntlets, PVC separators, as well as the complete battery using state-of-the-art industry standard machinery. With telecoms being one of its main focus areas, it has built up an impressive portfolio of clients that include BSNL, Indus Towers, Idea Cellular, Aircel, Viom and Huawei.
TowerXchange: Please introduce your role and background.
Dr Mike McDonagh, Technical Head, Microtex:
I have worked in the energy storage and battery industry since 1977, with broad experience covering design, manufacturing and applications of both lead acid and lithium ion batteries. I approach my role with a thorough grounding in electrochemical and materials science but also practical hands-on experience.
In addition to having more than 30 years of practical experience manufacturing and designing lead/acid batteries for automotive and industrial applications, I was also responsible for building and managing several battery plants in the UK. I was also the chief of R&D as well as production manager for many leading battery companies, such as Oldham Crompton Battery and FIAMM UK.
TowerXchange: Please tell us about Microtex– where does it fit in the telecoms infrastructure ecosystem?
Dr Mike McDonagh, Technical Head, Microtex:
Microtex was established in 1969 and manufactures industrial lead acid batteries for different segments: telecom, railways, nuclear and power facilities and material handling equipment.
There are about 400,000 telecom towers in India and we have a market share of about 2.6%. Microtex developed VRLA batteries for telecoms in 2007. Since then we have supplied VRLA battery sets to BSNL, Indus Towers, Idea Cellular, Huawei, Aircel and Viom.
TowerXchange: The first question our readers will want to know is ‘how proven is the solution in the field’ – please tell us about the performance of your solution in the field – who is using it and what results have been achieved?
Dr Mike McDonagh, Technical Head, Microtex:
Initially the sets were housed in air-conditioned enclosures which gave good life and was typically an ideal condition for the battery. However, the demand from the industry was to move to covered shelters without air conditioning. Our batteries were redesigned to withstand India’s high temperatures which sometimes can reach 50°C during summer.
This was achieved by using a superior blend of corrosion-resistant lead alloys of the positive plate in the cycle life. Batteries were also subjected to frequent deep discharges and often replacing the DG sets altogether. This called for a complete redesign of the battery from a purely standby design, to a cyclic application using flat plate AGM VRLA in place of the higher priced TGel battery.
The connectors and special terminals were designed to meet the current carrying requirements for deep cycle applications, meeting C3.33 rate of discharge.
The vent valve which is often ignored, is a critical component like the heart of the battery; Microtex gets its vent valves specially manufactured with a German supplier whose consistent valve opening and closing at the right pressure ensure no water loss takes place leading to cell dry outs, which causes thermal runaway. A common cause of failure in this type of battery.
Our major customer BSNL trusts Microtex for its MSC (Mobile Switching Centre) sites with several installations of 48v 1000Ah to 5000Ah. Typically, only the best products are used for MSC sites for their reliability and dependency in a country where power failure is regular.
TowerXchange: Please compare the TCO for a fairly typical off-grid cell site running dual DGs with a similar site where your energy storage solutions have been installed.
Dr Mike McDonagh, Technical Head, Microtex:
The total cost of ownership is a difficult parameter to calculate. There are several reasons for this:
- The capital costs are dependent on the installation and financing costs which are variable depending on tower location and interest rates.
- Diesel fuel and electricity costs are variable.
- Different sites have their own requirements of autonomy and grid availability, depending on their specific location across India. For example, Bihar will have around seven hours on the grid compared to Gujarat which will have more than 21 hours of available mains electricity. These sites will require different capital investments for their power supply.
- Maintenance and fuel delivery costs are very different depending on the location.
Despite this, it can be demonstrated with an example that in many cases reducing dependency on diesel power and substituting stored mains energy will enable considerable monthly savings. Reducing the monthly running costs which include amortisation of the equipment and batteries will clearly reduce the total cost of ownership.
Looking at a typical tower with three base transceiver stations of around 2.5 to 3kw average demand, it is possible to make some simplified assumptions about the energy supply costs. These are not accurate costs for the reasons explained above but allow us to get a reasonably close to real estimate.
Assuming a 12-hour gap in the mains electricity supply we would expect the following equipment:
- Diesel generator, DG (10kW)
- Battery bank 48V 600 Ah
- Power interface unit PCI
- Switch mode power system (SMPS)
Total cost of equipment amounts to around INR500,000 (US$7,700) for which the battery will be around 30%.
Looking at doubling the battery size then using eight hours of battery time and halving the diesel time to four hours instead of eight gives a 30% increase in the amortisation, an extra INR162/day, but a decrease of INR 462.4 in energy costs.
The total saving per month is (462.4 – 162) x30 = INR9,012/month (US$140/month).
This is a total monthly saving which includes capital investment and therefore it does demonstrate in a simplistic way that the TCO is indeed reduced with the increased use of battery solutions. This can be extrapolated to completely remove the diesel generator to provide even lower cost of ownership.
Daily running costs
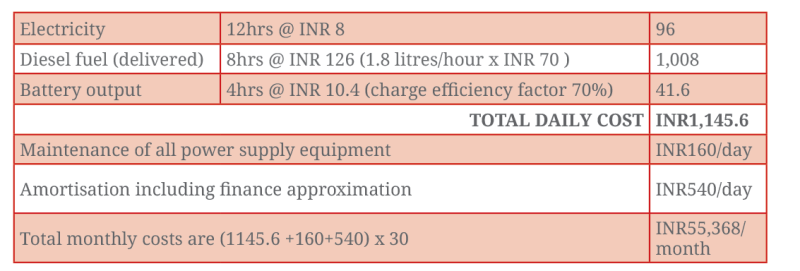
TowerXchange: How much tailoring to the specific requirements of individual sites can really be achieved through the selection of the right energy storage solution?
Dr Mike McDonagh, Technical Head, Microtex:
The important parameters to measure for any specific site are the available energy supplies (eg. solar, wind, hydro-electricity, diesel et cetera). The remoteness of the area and ease of access are also critical in choosing the energy supply – filling a diesel tank from a supply tanker for instance may not be possible.
The cost of running and the capital investment are major considerations. In a remote site with no mains electricity, where there is abundant daylight and mostly sunshine it makes sense to install an automated solar supply with battery storage. In less obvious cases, there may be hybrid solutions where the cost of the electricity is key to the size of the battery installation. In the example of a diesel hybrid using solar energy storage, the cost of running a diesel engine is high so a larger capital investment in the battery/solar segment would make sense.
In order to maximise the benefits, the type of energy storage and the size are critical components of the equation. At night, the runtime of the battery depends on its capacity (size) and the output (again size) of the solar panels. The lifetime of the battery is also important to calculate the running costs, eg. a 4-year battery life compared with an 8-year life for a more expensive battery. In this case the less expensive battery needs to be replaced twice as often and the amortisation cost may be higher.
Microtex can advise the optimum solution for a particular customer’s needs based on initial capital budget, running costs and maintenance costs. In the latter case, the location and access to personnel are key factors, whereas the capital cost of a battery and energy supply depend upon the autonomy of the site and the depth of discharge (DOD) the battery will undergo. The larger the battery the lower the DOD for a given autonomy and the longer the battery will last. If maintenance is not possible then the type of battery chosen should not need topping up and the AGM VRLA lead acid version will be specified. In case of deep cyclic applications tubular gel VRLA battery will be recommended.
Battery chemistries other than lead acid can be considered but Microtex recommends that for most installations, lead acid batteries are usually the most effective option given their stability over a wide range of temperatures, safety and their lower costs.
Lead acid being completely recyclable allows for effective pollution control. As many other chemistries do not have the option of recycling and usually end up in landfills leading to a growing battery waste problem.
TowerXchange: What is unique about your energy storage chemistry?
Dr Mike McDonagh, Technical Head, Microtex:
There are several established battery chemistries which can be used for energy storage and supply or even backup emergency power. These are sealed valve regulated lead acid (VRLA), open or flooded lead acid, nickel metal hydride/cadmium (NiMH/NiCd) or Li-ion types such as LiFePO4, LiCo, LiNMC et cetera. Right now Microtex promotes lead acid variants as the most reliable, safe and cost-effective energy storage solution for most telecom applications, but has the capability of providing any of the commercially available battery chemistries which it has approved.
Our lead acid batteries are uniquely designed to give optimal performance in terms of life and efficiency of operation. There are several important criteria to consider when choosing a battery for a particular site or operating pattern:
- The operating load and the length of time
- The availability and amount of energy for charging the battery
- The cost of the energy (diesel, renewable, grid, et cetera)
- The cycle life and calendar life of the battery
- The cost and capability for battery maintenance on the site
- The efficiency of the ratio battery output to battery charge
Without going into too much detail, a lead acid battery consists of lead compounds (active material) held in place by a lead alloy grid which also acts as the conductor (plates), all of which are immersed in sulphuric acid (electrolyte) separated by a porous membrane (separator). The positive plate has active material made of a porous lead dioxide and the negative is a spongy pure lead when in the fully charged state. During discharge both plates react with the acid to form porous lead sulphate.
All lead acid batteries operate the same way – what differentiates the Microtex brand are the unique design and compositions used in the grid alloy, the active materials of the plates and the separators. The balance of active materials used in the plates which provide the electricity have to be carefully balanced, the exact balance required depends upon the application: the depth and rate of discharge and recharge, the number of times it will cycle in a week, the calendar life expected, the depth of the discharges, the length of time of any idle periods, the operating temperature all are fundamental factors for which there is not a one size fits all solution.
Microtex has developed a range of grid alloys which are a unique blend of stiffness to provide a strong abuse resistant grid suitable for higher operating temperatures, as well as a low electrical resistance which maximises the recharge efficiency to give lower operational costs. The alloys for flooded cells and sealed VRLA cells are not the same. Microtex, unlike the majority of its competitors actually manufactures its own grid alloys which it has developed over decades and is still carrying out trials and tests for ongoing improvement. Likewise, unlike its competitors Microtex also manufactures other critical components such as the separators and cell boxes in order to optimise their properties in line with its field experience and own laboratory research.
Other components such as the terminals which connect to the intercell and supply cables are uniquely designed to prevent loosening during heating and cooling cycles of charging and discharging as well as day and night temperature variations. They also ensure minimal resistance at connection joints to ensure minimal resistance and energy losses through raised voltages or temperature
Another factor which should be considered for series parallel connected cells is the cell-to-cell variation which can lead to damaging imbalances between cells over time. This can result in over-discharge of some cells and overcharge of others leading to early battery failure.
Microtex has optimised its production methods to ensure that the absolute minimal variation is obtained in every single component to give the lowest possible difference between its finished cells. This is backed up by a stringent, nationally accredited quality control procedure and extensive product testing in our laboratories.
TowerXchange: Is a different energy storage chemistry the optimal choice for different cell site scenarios? In what typical scenarios will your solution perform best relative to alternatives?
Dr. Mike McDonagh, Technical Head, Microtex:
Microtex has a range of lead acid designs which should cover all telecom site requirements with advantageous properties compared with alternative chemistries. These are essentially summarised as follows:
Remote applications with high temperature variation
We have a range of sealed VRLA batteries which have high efficiency charge/discharge ratios, as well as being maintenance free and give good performance over a wider temperature range than alternative chemistries
Populated locations with on-site maintenance and low capital budget
In this situation Microtex can supply flooded or VRLA alternatives to suit the budget. Maintenance for the lower cost flooded range would require occasional water additions, for this range we have optimised the battery grid chemistry to minimise the water loss through gassing on charge. This means fewer occasions for topping up the battery which reduces the maintenance costs, we also can fit automatic watering systems to remove this cost. However, the cost of distilled water and the controls needed to prevent gassing and stratification mean that usually the VRLA option is preferred.
Safety as well as cost are also important in this scenario and lead acid is still regarded as the safest and most stable energy storage chemistry
Remote applications with a renewable energy such as solar panels
The VRLA battery made by Microtex is highly efficient on charge with a lower ratio of on-charge/discharge voltage ratio. This means you get more energy from the same restricted energy supply from a fixed size of battery. Other chemistries such as li-ion are very efficient but will cost around five times as much as an equivalent lead acid installation and will always have the question of how to recycle at the end of life.
TowerXchange: What can be done to protect against battery theft?
Dr. Mike McDonagh, Technical Head, Microtex:
Very little I’m afraid; there is no stopping a determined thief. Microtex has looked at several solutions but has not yet found a satisfactory and affordable option. However, we are very aware of this problem and we are actively working with other companies in the security field to find suitable cost-effective solutions to this problem. One solution used by another manufacturer is to put battery installations underground. This is just one of the options which Microtex are examining.
TowerXchange: Please sum up how you would differentiate your solution from your competitors’?
Dr. Mike McDonagh, Technical Head, Microtex:
There are several aspects of the Microtex products which set it apart from the competition.
The lead alloys used for the grids are manufactured and designed specifically by the company
to meet the demands of different end applications. Most lead acid battery companies buy standard alloys from a lead recycling company for their grid production.
The active materials in the electrodes have unique additive blends which enhance the battery performance. These additive blends have been formulated over decades of field and laboratory research to provide optimum battery performance in all the diverse market applications.
The connector and battery poles are designed to minimise resistance losses and inefficiency which improves energy capture and reduces costs.
Apart from the product differentiators, Microtex has extensive experience and knowledge to provide the best possible solutions and advice to customers in this market.
It is true to say that Microtex has unique experience both in the field and within its technical staff, which have combined to produce a battery with the best possible balance of materials for battery performance and life in most telecom applications. We do not believe any other company could match this.