In the quest to reduce DG runtime and OPEX, an increasing proportion of cell sites which previously ran dual Diesel Gensets (DGs) 24/7 are now combining Charge Discharge Cycle (CDC) batteries with a diesel genset – in many cases with the battery bank becoming the primary source of power. In order to understand the economics of this transition, and the relative merits of different energy storage solutions, TowerXchange spoke to market leaders EnerSys®.TowerXchange: Please re-introduce EnerSys® for any readers unfamiliar with your company.
Cheng Heng Hong, Vice President Sales & Marketing, Asia and Robert Pounder – Reserve Power Marketing Director, Asia, EnerSys®:
EnerSys® is the global leader in stored energy solutions for industrial applications in reserve power, motive power, aerospace and defense. Our extensive range of quality products includes Premium Thin Plate Pure Lead, Tubular OPzV and OPzS, Ni-Cad, Li-Ion and outdoor cabinet enclosures.With over 125 years’ experience in battery manufacturing, EnerSys® is the proven leader and innovator in reserve power batteries with customer-centric solutions. As mobile telephone networks evolve and continue to rapidly expand in emerging markets, there is great demand for reliable, improved power capacity solutions that can perform in harsh conditions. EnerSys® works in close partnership with leading companies and offers complete answers to a diverse range of telecom applications requiring stored energy. As part of the offering of energy storage solutions we also provide online support tools such as the battery sizing program (BSP). BSP is an advanced battery sizing engine with a built in battery layout configuration tool for all critical applications such as telecom, data center, rail and utilities. It also includes advanced calculations for use with telecom including hybrid sites. Together with our customers we effect smart decisions which combine our expertise and service with leading products resulting in the most effective, powerful and reliable energy storage technology available. TowerXchange: Please compare the TCO for a fairly typical off grid cell site running dual DGs with a similar site where deep cycle batteries have been installed.
Cheng Heng Hong, and Robert Pounder, EnerSys®:
Compared to sites running on dual DGs, a site with single DG having cyclic batteries as back up generates savings if the batteries were actually used for longer duties.
While a battery with cyclic capability is important, it is equally important to size the battery to maximise OPEX savings balanced with a calendar life that reflects the rate of cyclic usage and the charge acceptance capability of the battery. Typically a three year calendar life is desired before a battery is replaced, therefore based on one cycle per day the battery requirement is thus approximately 1,100 cycles life. For EnerSys® TPPL SBS Eon technology this number of cycles equates to a percentage depth of discharge (DOD) of approximately 75%.The example below gives a comparison of a site running 24/7 on diesel genset compared to a genset/battery hybrid. It also gives a comparison of different lead acid technologies with EnerSys® TPPL (SBS Eon Technology) providing the greatest OPEX savings. The result is reduced OPEX cost through reduced generator runtime and therefore reduced fuel consumption, extended generator maintenance intervals, reduced storage space, reduced transport and installation costs.
Even further reduction of TCO can be seen from a hybrid site that employs a second input of power, such as Solar PV. This significantly increases battery life. Often we offer pure lead battery solutions, which could more efficiently capture any additional surplus energy from the sun or DG by using a higher charge regime which will in turn increase the site efficiency, thus less DG run hours.
Case study example of DG/battery hybrid comparison with DG (24/7)
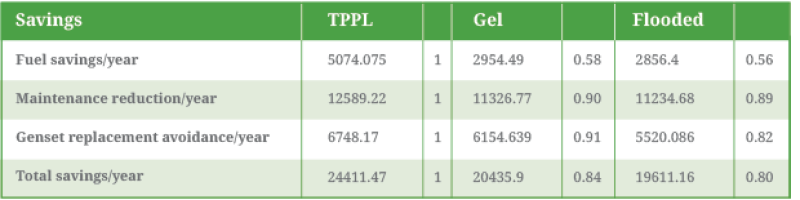
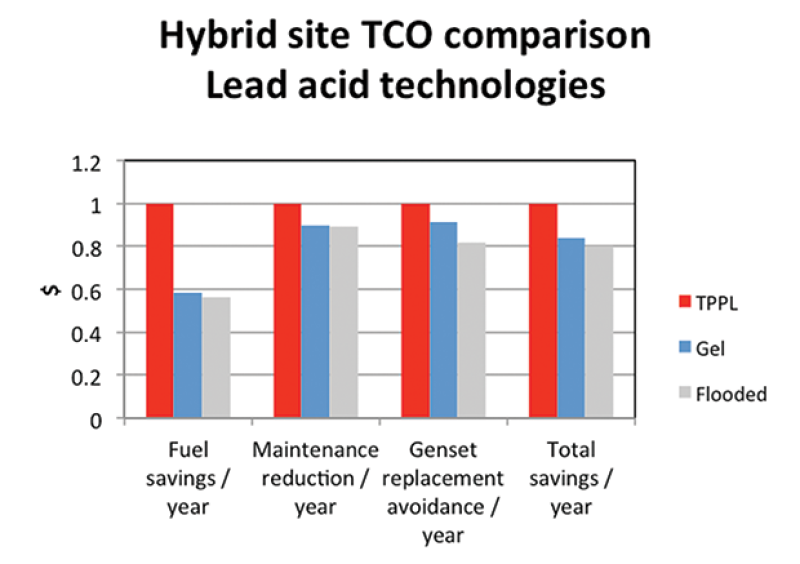
Cheng Heng Hong, and Robert Pounder, EnerSys®:
In the TCO comparison above, the battery has become the primary power source with for example, the TPPL SBS Eon Technology battery providing back up for 17.25hrs (72%) per day and genset 6.75hrs (28%) per day. In this scenario, the number of cycles provided by the battery is approx 2,700 with 2.16 cycles per day and a calendar life of approximately 3.4 years.
The concept is therefore to use the battery in a cyclic operation instead of a standard float backup. The system would typically control the discharge of the battery every day during the night, and recharge using the DG during the day.
Significant fuel and maintenance costs are saved, and that payback would justify such an investment.
How this can be made possible? This application of battery is classed as cyclic, used in partial state of charge, which means not each cycle will return the battery to 100% state of charge, thus enabling more diesel savings.
The thin-plate grids in TPPL batteries offer greater plate surface area and shortened ionic pathways, resulting in an overall reduction in internal impedance. With lower impedance, the TPPL batteries sustain a higher average voltage on constant power discharge. Additionally, reduced impedance allows the batteries to be charged in about half the time of conventional batteries, without sustaining damaging effects. Therefore TPPL batteries are suitable to use in a partial state of charge condition.
reduced impedance allows the batteries to be charged in about half the time of conventional batteries, without sustaining damaging effects. Therefore TPPL batteries are suitable to use in a partial state of charge condition
In summary, the following key advantages of TPPL batteries make EnerSys® PowerSafe SBS an excellent choice for hybrid applications:
PSOC (Partial Stage of Charge) compliant
Up to 1,800 cycles (50% DOD) with operating temperature up to 50C
Recharge time < 2 hours (50% DOD, 2.4Vpc, 1.0C10 re-charge current)
Low self discharge – 24 months shelf life
Up to 50% more capacity (in same foot print compared to tubular gel OPzV)
15 years design life according to Eurobat
Wide operating temperature range (-40°C to +50°C)
Made in Europe and USA
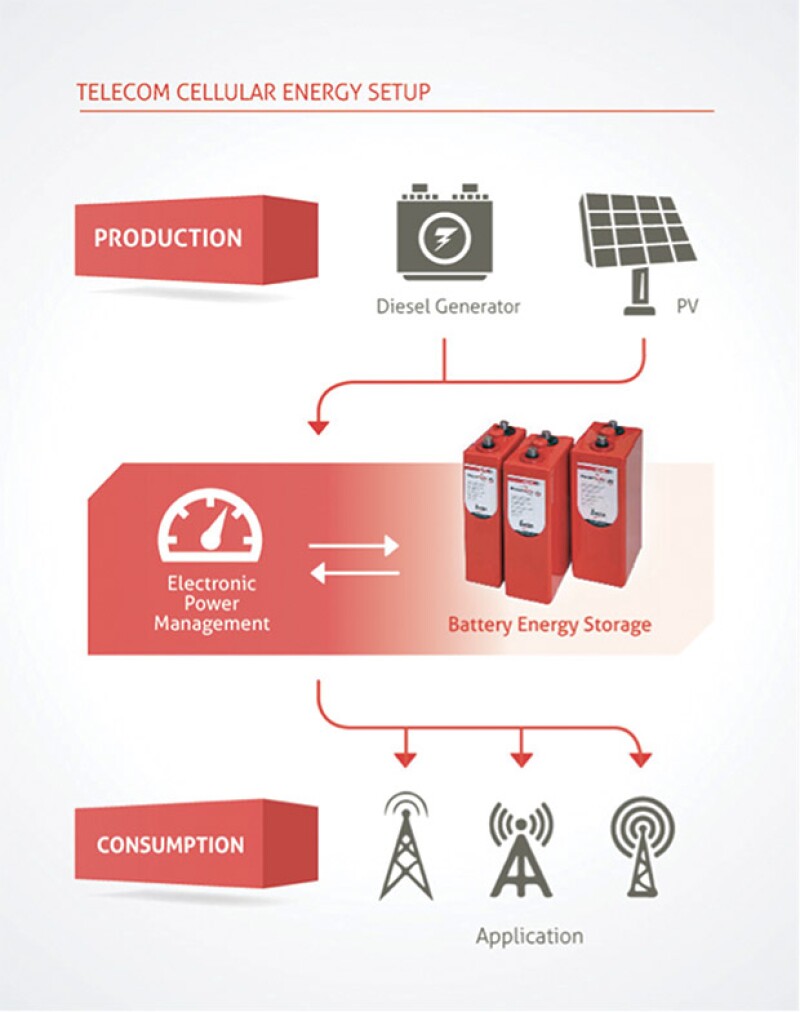
TowerXchange: Forgive my being rude, but it’s often suggested that lead acid battery manufacturers’ warranties are meaningless as they require compliance with installation and usage guidelines that are not practical in an emerging market context. How does EnerSys® ensure your warranty is more meaningful?
Cheng Heng Hong, and Robert Pounder, EnerSys®: EnerSys®
works very closely with project partners to ensure that the requirements to fulfill the warranty terms and conditions reflect the practical capabilities of the system and application, i.e. duty cycle control features, system monitoring, data recording.
We are involved from design, implementation to a complete end to end solution. This ensures having the right products together with other peripheral equipment such as the enclosure, systems, distribution and controllers that suit the application and environment.
EnerSys® has a flexible approach to the primary and secondary control features of the Charge/Discharge Cycle (CDC) that allow the tower owner to optimise the operating strategy to suit the limitations of the system and in addition, extensive testing allows EnerSys® to provide the user with preferential warranty terms whilst minimising risk. For hybrid applications, we have separate manuals which are different from ones we use for normal float charge applications. We also educate our users on using the products, provide training and offer maintenance program.
There must be a reason why EnerSys® is a global leader in stored energy solutions, and remain strong after 125 years. We deliver what we promise. EnerSys® manufactures and supplies the highest quality and most reliable products in our chosen markets and then consistently meet and strive to exceed our customers for service, technical support and value for money. Our warranty is backed up by sales and manufacturing locations in over 100 countries around the world.TowerXchange: Please share one or two examples of tower portfolios where EnerSys®’ energy storage solutions have been installed.
Cheng Heng Hong, and Robert Pounder, EnerSys®:
As we are unable to name our customers, I can only cite a few of these examples.
We successfully supplied over 40,000 blocks of EnerSys® PowerSafe SBS Eon Technology to several of Indonesia’s largest telecommunication networks and services providers utilising the ruggedness of the SBS Eon Technology’s characteristics.Another success story comes from our tireless effort in Myanmar whereby over 8,000 blocks of EnerSys® batteries were supplied to over 600 sites with various on-grid and off-grid conditions, including hybrid applications. These are only the orders received from the first entry phase of installation in Myanmar, we are working toward upcoming projects too.The mission was made possible through joint efforts between distributors and EnerSys®. This demonstrates our commitment by working closely with users to understand and meet all technical requirements. EnerSys® is now the preferred supplier for unstable grid applications to the operators and the installation base of EnerSys® batteries has continued to grow.TowerXchange: Finally, please sum up how you would differentiate EnerSys® from other energy storage solution providers
Cheng Heng Hong, and Robert Pounder, EnerSys®:
EnerSys® has a global and worldwide presence and coverage through its own subsidiaries in all continents – Americas, Europe, Africa, Middle East and Asia-Pacific.In Asia, EnerSys® has presence in seven countries and 18 local offices for sales and application support. We have a comprehensive product range and access to all commonly used battery technologies and are therefore in a position to help end-users to the most cost-effective (TCO) solution technically and commercially.
EnerSys® has 17 research laboratories situated in the USA, Europe and Asia and are constantly looking for new chemistries, plastics, separators and advanced technologies. It is our mission to ensure these new technologies are able to work together to form a battery with an expected life. Process improvements, measuring consistency in the manufacturing cycle is also a major part of the engineering and research teams effort to maintain the higher standards that EnerSys® sets for itself.