What are your towers worth? Whether you’re buying or selling assets, investing in transactions or supplying towers, it’s useful to know how towers are surveyed and evaluated, particularly in the context of emerging market tower transactions for which the documentation on towers may be incomplete or untrustworthy. We spoke to Henrik Kamstrup, one of four founders of Intelli Towers, a new analysis and design engineering firm with longtime experience and which specialises in this field.
TowerXchange: Where does Intelli Towers fit in the telecom tower ecosystem?
Henrik Kamstrup, Partner, Intelli Towers:
Launched in summer 2013, Intelli Towers is a specialist analysis and design engineering company, focusing on tower design and upgrade, and providing tower manufacture through partners.
Intelli Towers brings together four prominent tower design experts with many years of experience of the design, manufacture, rollout, and upgrade of passive infrastructure. Three of us have worked together before as owners of KPR Consult; a tower engineering company specialist established 10 years ago - KPR are leaders in analysis, strengthening and co-location management of telecom towers in Nordic regions.
We have an extensive database and experience of just about every possible tower design in every global tower market except the US. We’ve analysed thousands of towers since 2006 - we know every type of tower, rooftop, monopole, guyed mast, angular or tubular lattice tower.
No market is new to us when it comes to tower design and strengthening; emerging market towers are not especially different - everywhere uses the same American standards. What does differ is how to implement reinforcement and what to do with foundations - much depends on local manpower, and on availability of machinery or whether it’s just shovels and wheel barrows!
We get a lot of requests from MNOs and towercos asking us to train their subcontractors on how to strengthen towers, and what to do with old, rusty towers. So we’ll often run a ‘what to do and how to do it’ session, then monitor them for a couple of weeks afterwards.
TowerXchange: How do you audit a portfolio of towers, particularly audits by towercos seeking to evaluate the lease revenue generating potential of acquisitions?
Henrik Kamstrup, Partner, Intelli Towers:
Capacity and lifetime are relevant for the business case.
Initially we have to group the sites into well documented and not-well documented. These have to be handled differently.
Our audit will group the sites into safe or not safe. If not safe, can we bring it to safe conditions for a fair cost, and if safe does the site has potential for upgrading for more tenants for a fair cost?
If time is not available to fulfill all before closing, some assumptions can be implanted in the contract and verified in a window just afterward.
TowerXchange: How complete is the documentation on the towers you survey?
Henrik Kamstrup, Partner, Intelli Towers:
In our experience, elder towers are seldom well documented. We’ve worked from a lot of incomplete and untrustworthy documentation. Sometimes we’ll only have complete documentation on 10-20% of sites - anything around 50% is a good number.
However, for a very quick overview we can trust relevant pictures showing the existing configuration of the tower - sometimes these can be even more useful than existing drawings as antenna loading seldom are updated on drawings. We have a database of thousands of different types of towers, and can find a similar structure very fast. Based on a good photo we can make a first step in the evaluation, even before knowing strength of the members.
TowerXchange: What does it cost and how long does it take to evaluate towers for acquisition?
Henrik Kamstrup, Partner, Intelli Towers:
It depends on how detailed you want it.
Assuming a portfolio of 1,000 towers we can make an overall theoretical audit based on existing documentation supplemented with photo within one month. This can be done for less than US$500 per site.
For a full audit for 1,000 towers with a “normal” share of non-well documented sites where surveys are requested, it will cost less than US$2,000 for the well documented sites and up to double for the non-well documented sites, including proposals for how to extend the use of the towers. And this will take approximately six months.
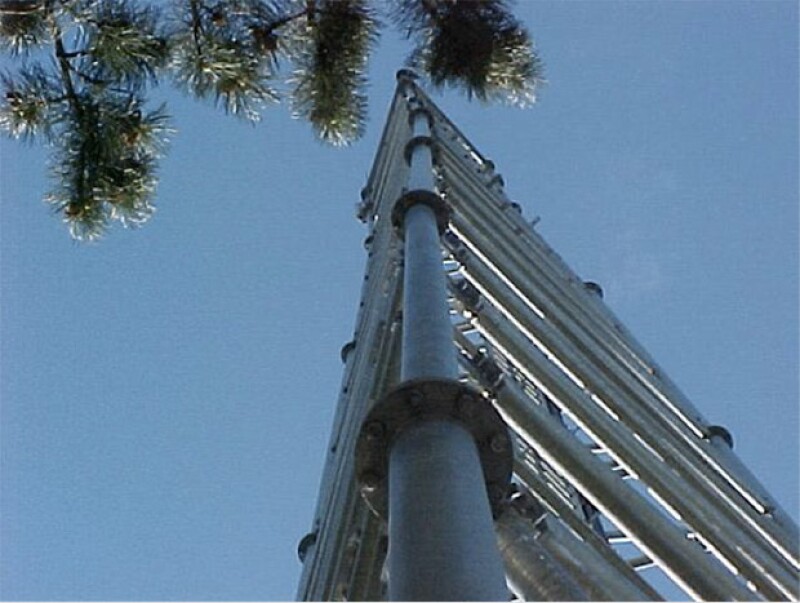
TowerXchange: Is there an opportunity for sellers to evaluate and upgrade towers before they are brought to market to maximise their value?
Henrik Kamstrup, Partner, Intelli Towers:
Absolutely. A couple of the operators we met at the TowerXchange Meetup also showed interest in potential evaluation and upgrade of their towers before they sell - they realised that for a limited cost they can gain significant extra capacity and add value to their towers. Further, the tower documentation package will be 100% updated which also adds value to the transaction.
If upgrading for more tenants it is important to select the sites where it is an advantage without doubt as you don’t know the buyers plans.
TowerXchange: What masts and towers are suitable for upgrading capacity for multiple tenants, and which aren’t?
Henrik Kamstrup, Partner, Intelli Towers:
The simpler a structure is, the simpler it is to upgrade. Any kind of lattice tower is simple to upgrade. For complex lattice towers (such as power lines types) you can change members from slim to large, but it is relatively difficult to gain significant extra capacity by adding extra structural members.
Guy masts are difficult to reinforce. You can change the placement of feeder cables, thus decreasing the wind load from outside and gaining strength, but you can only create a limited amount of capacity. Similarly reinforcing monopoles can be done, but it’s difficult and often expensive.
Upgrading foundations can be more complex, especially if you need new flooring, and a new surface. The major challenge in emerging countries is the verification of the actual used rebar in the concrete. There are several ways of detecting this but also to upgrade the existing non-trusted foundation to a new fully compliant foundation. We show and explain these solutions to clients from project to project depending on the current challenge.
TowerXchange: Under what circumstances is the replacement of a tower a better option than upgrade?
Henrik Kamstrup, Partner, Intelli Towers:
If the general condition of the tower is poor. And if the costs for strengthening will be close to a new tower, or the strengthening will create a tower difficult to maintain. Or if you have an unsafe tower where you have to invest, then you might set up a new tower with capacity for more tenants.
Let me give you some examples: We’ve seen some poorly installed towers. It can be easy to tell; if you look up a leg and see the alignment, it should be a straight vertical line. If it’s buckled, the initial assembly was potentially poor, and it will probably fail a towerco’s acceptance criteria. I’ve seen towers assembled with bolts missing, or dirt/small rocks in the flanges, which can affect the pre-tensioning of the bolts after 6-12 months.
The other main issue is corrosion. Some rusty towers can have their lifetimes extended by replacing all the bolts, but if all main members are weak, the only option may be taking the tower down or to make expensive investments in upgrading.
We very occasionally see examples of poor manufacturing quality, such as poor welding, but we seldom encounter this - each member has to be effectively tied together, otherwise they can’t move on to the next!
TowerXchange: How do you evaluate and upgrade tower foundations?
Henrik Kamstrup, Partner, Intelli Towers:
It varies as there are different types of foundations. Some have huge slabs you can see above ground, when they’re underground you have to dig to evaluate depth. We often have to evaluate concrete reinforcement by hammering off a piece and verifying.
Again upgrade options vary according to the type of foundation. We have to be quite creative to rebuild around the existing foundation to ensure a site with upgraded capacity is safe. For example, we can add to an existing lump of concrete foundation, using it as ballast, adding brackets on two sides and drilled into foundations. Just adding 30-50cm of concrete, 1m deep, on two connected sides can add a lot of capacity. Or if necessary we can take the outside layer off across the whole length and add reinforcement. A lot depends on the soil and on the ground water level of course.
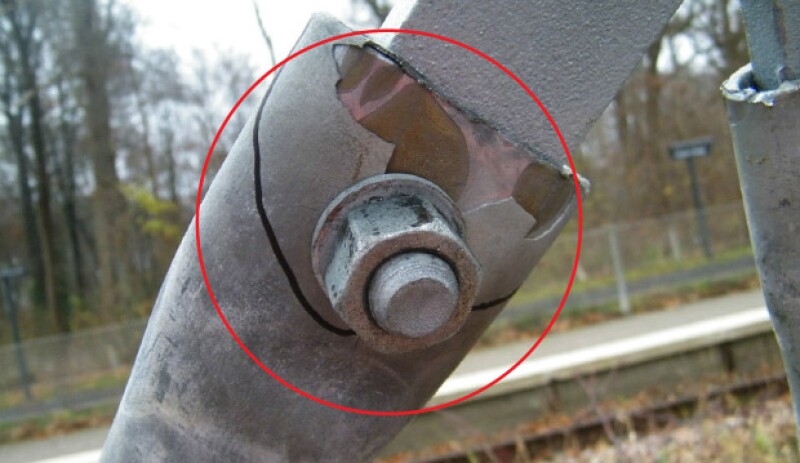
TowerXchange: What’s your view of the potential of reusable steel foundations?
Henrik Kamstrup, Partner, Intelli Towers:
While we do a lot of work evaluating and upgrading concrete foundations, one of our visions for the tower industry is to evangelise the use of innovative reusable steel foundations.
It takes just a few days to implement a steel foundation. The steel foundation comes in the same shipping container as the tower, which makes logistics easier. We’re particularly keen on steel foundations that use the soil as ballast, with a three arm steel frame extending 1.5m below terrain level. Each of the three arms stands on thin steel membrane elastic enough to move with the soil.
What’s great about these foundations is that if you need to move a tower, for example if you have a problem with the landlord, it’s movable at a cost of only limited man-hours (no extra material costs).
The price of a steel foundation can for some systems be 15-20% less than concrete. It’s easy to install but it does require more space, why it’s best for suburban and rural sites.
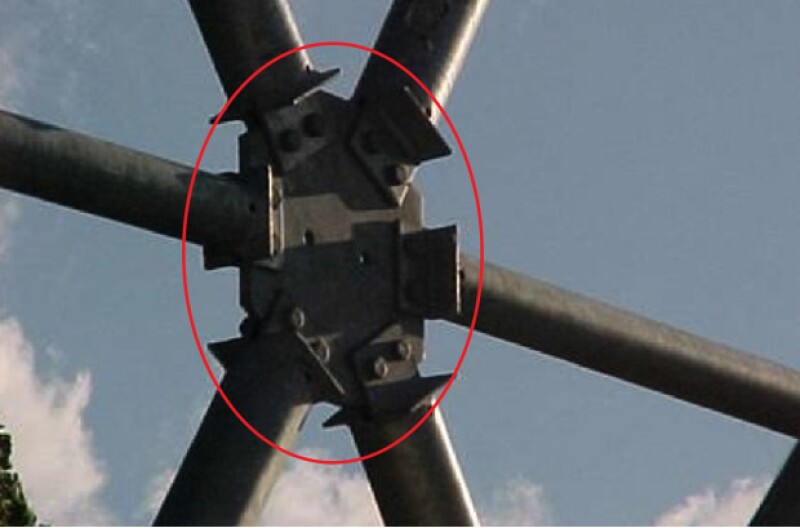
TowerXchange: How can innovative tower designs help overcome difficulties securing permits?
Henrik Kamstrup, Partner, Intelli Towers:
In markets such as Russia it can be difficult to get permanent building permits, but you can install temporary tower solutions as long as foundations don’t exceed 50cm below terrain level.
Using a steel foundation with a standard concrete roadblock for ballast under each leg, you can erect a 40m tower. Such a structure could have a long lifetime - they’ll stand up to gust wind - but would still be classified as a temporary structure by permit issuers.
If you want to achieve the maximum loading at the minimum cost, you need professional assistance when setting up the specs
TowerXchange: How can towercos and MNOs ensure the design of new towers best meets their requirements?
Henrik Kamstrup, Partner, Intelli Towers:
If you want to achieve the maximum loading at the minimum cost, you need professional assistance when setting up the specs in order to ensure that all important aspects (e.g. updated norms, relevant wind speeds, effective equipment loading and placement et cetera) are taken into account. Having the right professional sparring partner setting up these requirements (also discussing optimal solutions for future loadings) secure the optimal specs.
When offers are coming in it is also important to have professional assistance evaluating how the proposed towers fulfill the specs.
TowerXchange: Finally, please sum up how you would differentiate Intelli Towers from other tower design and service companies.
Henrik Kamstrup, Partner, Intelli Towers:
Intelli Towers are 100% dedicated for towers and uses innovative designs to deliver the maximum capacity at minimum cost. We work within the rules, norms, codes and standards to ensure quality and safety, but we know the tricks to place equipment in certain positions to gain capacity.
We’re very focused on working with our clients and meeting our clients’ needs - if we say we’ll do it, we’ll do it on time.
It’s important that we’re independent - we don’t manufacture towers. Tower manufacturers have their own engineering department, and they’re focused on selling what they have and the structures they know. We know all different manufacturers’ structures, we know the different producers, and we have a wider range of experience.